A PRACTICAL FCM TRAINING TAILORED TO YOUR BUSINESS NEEDS
07 OCTOBER 2020
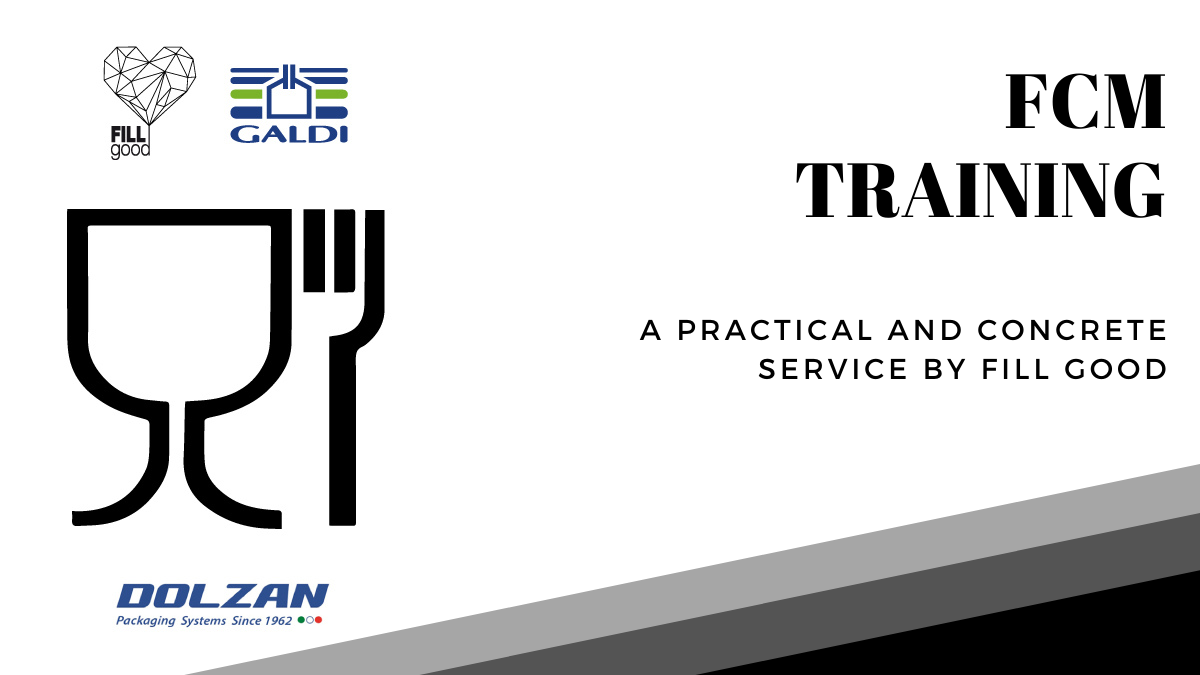
Specific training on Food Contact Materials (FCMs): this is a new service offered by FILL good in cooperation with Galdi.
Our aim is to provide support and advice to manufacturers of plastic, metal and silicon components for the food industry, and particularly to suppliers of dosing systems for dry food products.
So yes, it is a consulting service on FCMs, but one that sets itself apart from the rest.
OUR EXPERIENCE WITH DOLZAN
The idea for this service was born out of a need.
For many years, Galdi has been providing training on how to comply with - and adjust to - FCM directives for all its suppliers of components coming in direct contact with packaged products.
A few years ago, as our first packaging machines for dry food were being developed, we needed to find a supplier of dosers for this type of products.
So Galdi got in touch with Dolzan, already a trusted business partner. In turn, Dolzan asked Galdi for support with optimising its internal FCM management procedures in order to ensure the greatest chances of success.
Galdi and FILL good then started to put together a training tailored to the needs of their supplier, to make sure that its processes fully complied with FCM directives.
Dolzan was very receptive and adjusted quickly, assessing and implementing necessary compliance requirements too.
A PRACTICAL FCM TRAINING
Having worked with Galdi on the FCM compliance training and thanks to our experience with Dolzan, we realised that the only viable approach had to be hands-on and custom-made.
The first goal was to streamline the huge amount of information related to FCM regulations, so that quality and production managers can handle materials and components autonomously, in compliance with relevant directives. After all, they are the ones in charge with drawing up guidelines for operators, warehouse staff, suppliers and other personnel involved, ultimately making sure that procedures are implemented correctly.
Besides technical know-how, what managers really need is a practical work method, which they can then apply to their business.
FCM consultants are usually very knowledgeable about the theory. However, as a "company talking to another company", we wanted to focus more on the practical implementation of provisions inside and outside production facilities.
For this reason, FILL good decided that both a Galdi designer and our microbiologist would be in charge of the FCM training.
The former "puts himself in the customer's shoes" to identify areas, components and processes that incur the risk of fines. While the support provided by our experienced microbiologist is key to evaluate the hygienic standards in the facility with the same criteria used by inspectors.
This is not just training then: what we offer is a comprehensive FCM consulting service tailored to your business.
THE STAGES OF FILL GOOD'S FCM CONSULTING SERVICE
FILL good's FCM training has a structured outline, but timing is flexible and tailored to the needs of each individual company.
The service is made up of 4 stages:
AWARENESS-RAISING & TRAINING
Although this section is more focused on theory, we still adopt - as mentioned earlier - a practical approach.
The training begins with an overview of regulations on FCMs: Regulation CE 1935/2004, Regulation CE 2023/2006, Ministerial Decree 21/03/1973 and Reg.10/2011.
As our experts start to identify potential areas or elements that may lead to fines, the course also covers:
● the Catalogue of Sanctions for product contact materials.
● the principles to comply with Good Manufacturing Practice (GMP) guidelines.
SUPPORT
Using technical drawings, we locate, identify and quantify all machine components that come in direct contact with food. These are then classified according to material, as well as trade and product category.
PRACTICAL ACTIVITIES
This stage encompasses a number of activities, mainly involving warehouse management, including:
● an audit to highlight observed non-compliances
● support with registration of sites that manufacture/process/storage FCMs with competent authority (ASL in Italy)
● if needed, coordination with a laboratory for FCM testing, including migration tests, for the Declaration of Compliance.
EVALUATION
After a few months, we assess progress made in classification and traceability procedures.
In the first interim report submitted to quality managers, our consultants take stock of progress and suggest further actions. At the end of the training, they draw up a final report.
And, of course, you can always rely on their advice, even after the training is over, as they will be sharing recent developments and inform you about upcoming webinars.